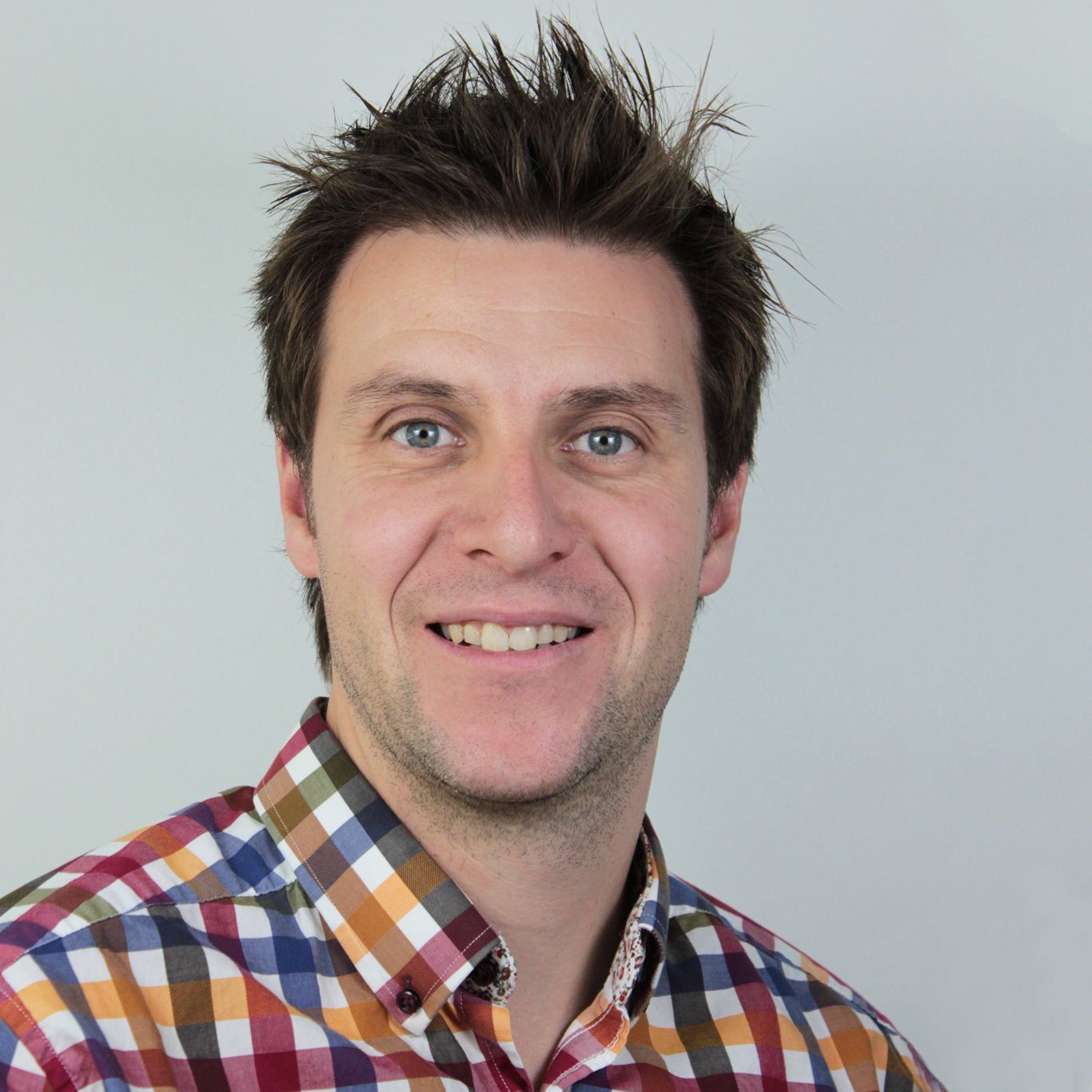
Auteur :
Vincent Lavoie, Chercheur Leader | Séchage du bois – FPInnovations pour Algorex
Le procédé de séchage du bois a évolué considérablement dans les dernières années. On n’a qu’à penser aux moyens de mesurer et de suivre la mesure de la teneur en humidité (TH), un indicateur important de la qualité du séchage. Aujourd’hui, à quelques exceptions près, les usines de rabotage possèdent un humidimètre en ligne pour mesurer la teneur en humidité de l’ensemble des pièces d’un lot de séchage. À l’intérieur des séchoirs, plusieurs industriels possèdent maintenant des systèmes de mesure diélectriques pour améliorer les arrêts des séchoirs, étape très importante pour maximiser qualité, productivité et consommation énergétique. Il est aussi maintenant possible de faire une estimation de la teneur en humidité à la sortie de l’usine de sciage en ayant comme information la masse des paquets ainsi que le volume de bois et l’essence considérée.
Il est également possible et plus que fortement recommandé de regrouper par lot les informations de grades et de teneur en humidité au planeur lorsqu’un système de traçabilité est implanté.
Plus récemment, nous avons vu l’intégration du suivi des conditions en temps réel avec la détection d’anomalies d’opération des séchoirs, qui permet de s’assurer du respect des conditions de séchage et d’optimiser la productivité des équipements.
Malgré cette évolution, la précision du séchage peut encore être améliorée. Des lots sont encore séchés sans être optimisés d’un point de vue qualité et/ou productivité et/ou efficacité énergétique.
Des pièces de casse-tête à assembler
Un défi important réside, à savoir l’intégration de toutes ces informations en un seul endroit où il devient possible de réaliser des analyses, des constats et des recommandations.
C’est comme si chacune des composantes d’information était une pièce de casse-tête. La plupart des usines possèdent l’ensemble des pièces mais celles-ci ne sont pas nécessairement assemblées.
Combien de fois en usine, lors d’interventions d’assistance technique sous forme d’accompagnement, il est nécessaire de fouiller à différents endroits pour obtenir l’information suivante :
- Composition du lot (souvent sur des rapports papier de chargements)
- Fraîcheur des paquets chargés sur les trains de chargement et durée séparant la formation des paquets au sciage et le rabotage (information souvent compilée à la main et souvent non utilisée)
- Programme de séchage utilisé et respect des conditions (graphique de séchage imprimé ou disponible dans le système de contrôle)
- Valeurs de teneur en humidité directes ou indirectes venant des équipements intégrés aux séchoirs et utilisées pour l’arrêt (dans le système de contrôle ou dans des fichiers Excel)
- Valeurs de la teneur en humidité des tests de validation à chaud avec humidimètres portables (sous forme papier ou fichier Excel)
- Durée du délai entre la fin du séchage et le rabotage
- Données sur la classification finale au planeur, sur la mesure de la teneur en humidité et sur la productivité au rabotage
L’information contenue dans toutes ces pièces du casse-tête permet de résoudre bien des problématiques reliées au séchage. La distribution des grades et de la teneur en humidité par chargement de séchage au rabotage permet de cibler après coup les chargements réussis et ceux problématiques et ainsi orienter des actions pour améliorer le procédé. Évidemment pour ce faire – on le répète – il est nécessaire de pouvoir faire la traçabilité des paquets au rabotage. C’est une pièce critique du casse-tête qui doit être priorisée par l’industrie pour faire progresser le procédé de séchage.
Commencer par juger de la réussite du séchage
La réussite d’un chargement de séchage réside dans le succès à atteindre un certain niveau de teneur en humidité et un contrôle sur un léger % de bois vert toléré, mais également sur la distribution des grades obtenus menant directement à une valeur de produit. Évidemment, les deux sont intimement liés. Le but de sécher le bois demeure de réduire la teneur en humidité au niveau requis par le marché. Trop de bois humide mènera au déclassement vers les grades inférieurs. D’un autre côté, nous savons que sursécher le bois provoquera davantage de défauts de séchage attribuables à des niveaux de retrait plus importants. L’arrêt des séchoirs au bon moment à la plus grande fréquence possible devient un élément clé du succès du séchage.
Pour statuer sur l’arrêt des séchoirs, on doit s’assurer d’analyser chacun des lots au planeur qui comportent un pourcentage de bois vert acceptable selon une cible établie. Les lots qui en possèdent plus que la limite fixée deviennent non conformes et il en va de même pour les lots qui n’en contiennent pas du tout.
On doit également fixer un critère de succès pour le grade. Ce critère doit être établi par chaque entreprise et en fonction de ses objectifs.
L’intégration des données de base et des bilans automatisés par lot sur la réussite du séchage en quelques clics à partir d’une même plateforme et par lot de séchoir devient donc nécessaire, voire l’outil à prioriser pour assister l’opération de séchage.
Les lots rencontrant à la fois les critères de conformité de la TH et du grade sont considérés comme un succès. On doit pouvoir faire des relations entre la matière première, la façon dont le bois a été séché, l’arrêt des séchoirs, les périodes d’entreposage et le succès du séchage. Ces conditions gagnantes deviendront un guide pour obtenir davantage de lots conformes. Une recette à succès peut être différente d’un produit à l’autre.
Les lots ne rencontrant pas le critère de teneur en humidité à la fin du séchage présentent une problématique d’arrêt des séchoirs. Une attention particulière doit être apportée entre la teneur en humidité mesurée aux séchoirs (soit par des systèmes intégrés ou par la validation à l’aide d’appareils portables) et la teneur en humidité mesurée dans le produit final au planeur.
Les lots ne rencontrant ni le critère de grade ni celui de teneur en humidité doivent dans un premier temps être rendus conformes pour la teneur en humidité. Une fois cela réglé, il y a de fortes chances que le grade soit amélioré. S’il ne l’est pas, il faut regarder du côté du surséchage et d’autres causes potentielles qui peuvent être ou non reliées au séchage. Et c’est là qu’un système intégré prend tout son sens car il permettra rapidement d’établir des causes potentielles qui pourront mener à des changements. C’est par des changements orientés par la connaissance du procédé qu’il sera possible d’améliorer l’opération et, par le fait même, les indicateurs clés de performance de l’entreprise.
Relier l’opération à l’entreprise
On a souvent tendance à mélanger « indicateur clé de performance » et « indicateur de performance de procédé », ou métrique opérationnelle. Un indicateur clé de performance est lié à la performance de l’entreprise, se situe à plus haut niveau, est utilisable pour plusieurs départements et est utilisé pour des décisions stratégiques d’entreprise. En contrepartie, un indicateur de performance de procédé ou une métrique opérationnelle est davantage lié à la performance d’un procédé spécifique.
Par exemple, la distribution des grades finaux au planeur est davantage un indicateur clé de performance pour l’entreprise alors que la distribution de la teneur en humidité finale des produits est davantage liée à un indicateur de performance du procédé de séchage.
Il existe évidemment des liens importants entre les deux et toute contribution à l’amélioration des indicateurs de performance liés à la distribution de la teneur en humidité finale contribuera à améliorer l’indicateur clé de performance sur les grades finaux.
Une bonne connaissance du procédé aidera à déterminer et prioriser les bons indicateurs de performance de procédé. Les spécialistes de procédé aideront grandement ce processus de priorisation et représenteront à cet égard une pièce maîtresse dans l’exercice global d’optimisation.
Suivre en parallèle les deux niveaux d’indicateurs de performance et les relier permettra une meilleure optimisation du procédé. Évidemment, des actions et des suivis seront nécessaires pour voir une évolution sur la performance.
En terminant, les outils, les connaissances du procédé, les actions et les suivis permettent l’amélioration globale des performances des procédés et de l’entreprise.